Ultralight &Ultrasafe -EOSMART- Original manufacturer of laser obstacle clearing equipment
1.Development and Production of laser obstacle remover
One of the core technologies of laser obstacle remover devices is laser cutting. The principle is based on focusing a high-energy-density laser beam onto an extremely small area, generating sufficient shock waves or heat to rapidly melt, vaporize, or ablate materials, thus achieving precise cutting. In the protection of high-voltage power lines, the application of laser cutting technology requires not only high precision but also stable operation in extreme environments. For example, the power density of the laser beam can reach 10^8 to 10^10 watts per square centimeter, enabling laser cutting to complete tasks with extremely high speed and precision when dealing with branches near high-voltage lines while minimizing the impact on the surrounding environment.
In practical applications, the cutting efficiency and accuracy of laser obstacle remover devices are achieved through a series of experiments and optimizations. For instance, by adjusting the frequency and energy of the laser, effective cutting can be performed on branches of different materials and thicknesses. In a case study involving high-voltage lines, the laser obstacle remover device can clear branches up to 10 centimeters in diameter in less than 5 minutes, with an accuracy error of no more than 1 millimeter, significantly enhancing the efficiency and safety of obstacle removal operations.
Moreover, laser cutting technology demonstrates unique advantages in environmental protection and sustainable development. Compared to traditional mechanical cutting or chemical removal methods, laser cutting does not produce harmful chemicals or solid waste, reducing environmental pollution. At the same time, the precise control technology of laser obstacle remover devices ensures minimal material waste, meeting modern environmental and resource-saving requirements. In the context of global climate change and frequent extreme weather events, environmental adaptability testing and optimization of laser obstacle remover devices are particularly important, ensuring stable operation under various climatic conditions and providing strong support for the stable power supply of the grid.
2.Laser Transmission Characteristics in Extreme Environments
In high-voltage line environments, the laser transmission characteristics of laser obstacle remover devices are key factors in their design and application. Electric and magnetic fields in high-voltage environments can interfere with the propagation of laser beams. Therefore, studying the transmission characteristics of lasers under these conditions is crucial for ensuring the accuracy and reliability of laser obstacle remover devices. The scattering and absorption properties of lasers in air also affect their transmission distance and energy density, especially under humid or foggy weather conditions, where the attenuation of laser energy is more pronounced. Through experimental data and case studies, we have found that using specific wavelengths of lasers, such as near-infrared lasers at 1080 nm, can reduce the impact of atmospheric scattering to some extent and improve transmission efficiency under adverse weather conditions.
3.Precise Control Technology of Laser Obstacle Remover Instruments
In the development of the laser obstacle remover—a guardian of high-voltage power grid lines—precise control technology is one of its core competitive advantages. By employing advanced laser cutting techniques, the laser obstacle remover can accurately remove branches and other obstructions that threaten line safety without touching the high-voltage conductors. For example, in an experiment focusing on the precise control technology of the laser obstacle remover, the device achieved cutting with a precision of 1 millimeter within 100 meters of high-voltage lines, a level of accuracy far surpassing traditional mechanical methods. Additionally, by integrating high-resolution cameras and image recognition algorithms, the laser obstacle remover can monitor and analyze the growth of branches in real time, thereby achieving precise planning of the cutting path.
Hardware System Development
1.Selection and Optimization of Laser Generators
In the development of laser obstacle remover devices, the selection and optimization of the laser generator are critical steps. Considering the special working environment of high-voltage power lines, the laser generator must have high stability and high-energy output characteristics to ensure stable operation under various extreme weather conditions. For example, to address the common issue of tree branch interference on high-voltage lines, we chose a fiber laser generator with a wavelength of 1080 nm, which offers excellent penetration and cutting efficiency. During the optimization process, we adopted an advanced thermal management system to reduce the risk of laser overheating caused by prolonged operation, thereby extending the lifespan of the equipment and maintaining its performance stability.
2.Design and Calibration of the Optical System
During the development of the laser obstacle remover device, the design and calibration of the optical system are crucial for ensuring the equipment performs tasks efficiently and accurately. Given the special environment of high-voltage power lines, the optical system must be able to adapt to extreme weather conditions while maintaining precise focusing and stable transmission of the laser beam. To achieve this, we used a high-power laser generator combined with advanced optical lens assemblies to minimize energy loss and enhance cutting efficiency.
During the design phase, we employed ZEMAX optical design software for simulation to optimize the optical path and ensure the accuracy of the laser beam at different distances and angles. For example, in simulations, we found that by adjusting the focal length of the lenses, the diameter of the laser beam could be controlled to within 500 micrometers, enabling precise cutting of fine branches.
In the design and calibration of the optical system, we not only relied on theoretical models but also conducted extensive experiments and field tests to continuously optimize system performance. Within a range of 10–500 meters, the lens’s focal length was electrically adjusted to form a virtual closed curve, ensuring that the laser obstacle remover device automatically focuses at different distances without manual intervention, reducing operational complexity. This makes it a reliable guardian for high-voltage power lines in practical applications.
3.Integration of the Robotic Pan-Tilt Head and Mobile Platform
During the development of the laser obstacle remover device, the Robotic Pan-Tilt Head is key to achieving efficient operation of the equipment. By adopting advanced robotic arm technology, the laser obstacle remover device can accurately locate and cut obstacles on high-voltage lines, such as branches, thus ensuring the stable operation of the power grid. The integrated Robotic Pan-Tilt Head has dual degrees of freedom, enabling precise motion trajectories to ensure that the laser beam reaches the designated cutting point without error.
In practical applications, the repeat positioning accuracy of the Robotic Pan-Tilt Head can reach 0.0001°, which is crucial for ensuring operational safety and efficiency. The Robotic Pan-Tilt Head endows the laser obstacle remover device with mobility in various terrains and environments, allowing it to adapt to complex on-site conditions. Additionally, the durability of the Robotic Pan-Tilt Head must be considered to withstand complex manual handling and installation, ensuring long-term trouble-free operation.
Software System Development
1.Control Software Architecture of the Laser Obstacle Remover Instrument
The control software architecture of the laser obstacle remover device is at the core of the entire equipment’s intelligence. It is responsible for coordinating the efficient operation of the laser generator, optical system, robotic arm, and mobile platform. In terms of design, the software architecture adopts a modular design principle, ensuring the system’s scalability and maintainability.
For example, by introducing advanced image algorithms, the laser obstacle remover device can clearly identify branches and obstacles around high-voltage lines with a recognition rate as high as 99%, significantly enhancing the efficiency and safety of obstacle removal operations. Additionally, it performs real-time detection of moving objects such as people. When a moving object enters the vicinity of the device, it can automatically detect and take action, reducing operational risks.
The control software also integrates tipping protection sensors, automatic distance measurement sensors, automatic focus algorithms, video recording mode, and photography mode. Innovative algorithms and models are key to turning imagination into practical solutions.
2.User Interface and Monitoring System
In the development of laser obstacle remover devices, the design of user interfaces and remote monitoring systems is crucial for ensuring ease of operation and real-time monitoring capabilities. The user interface should adopt an intuitive design to reduce the learning curve for operators and improve work efficiency. For example, using a graphical operation interface combined with touch screen technology can achieve rapid response and precise control.
Interface design should adhere to ergonomic principles to ensure clear visual feedback and a convenient interaction experience in various operating environments. Additionally, the remote monitoring system should integrate advanced data communication technologies, such as Wi-Fi connections, to ensure stable connectivity in remote or complex terrains. Real-time data transmission allows for real-time tracking of the laser obstacle remover device’s operational status, enabling timely responses to any potential issues.
Case studies show that when the remote monitoring system is combined with artificial intelligence algorithms, it can achieve fault prediction and automatic alarm functions, significantly enhancing the reliability and safety of the equipment. The design of user interfaces and remote monitoring systems not only concerns aesthetics and usability but also the efficient operation of the entire laser obstacle remover system and grid security.
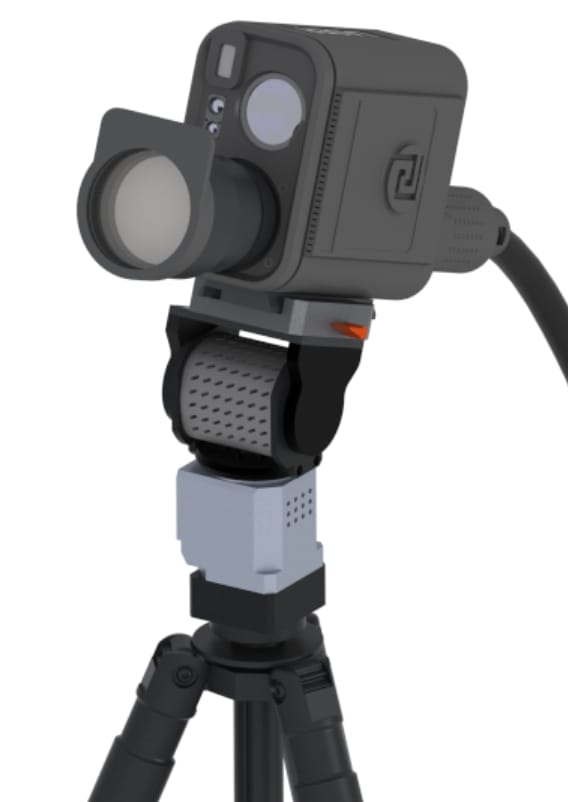
laser obstacle fucus head, laser shoot head
Portable lightweight laser obstacle remover of tree trimming
Laser obstacle remover of 250-1500 W for cutting tree branches